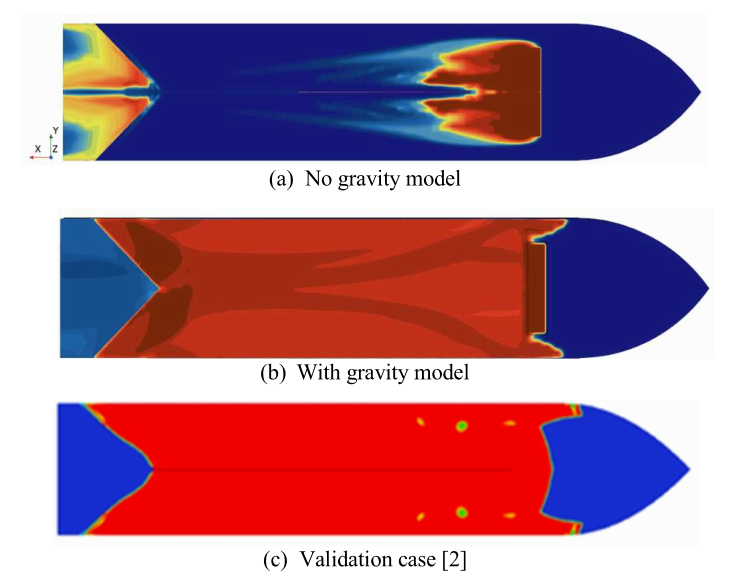
CFD Modelling of Air Lubrication Systems in Ships
Roya Shademani1, Tommi Mikkola1, Teemu Manderbacka1, Sasan Tavakoli2, Heikki Remes1
1Department of Mechanical engineering, Aalto University
2 University of Melbourne, Australia
Roya.shademani@aalto.fi
Presented at the 26th Numerical Towing Tank Symposium (NuTTS) – Duisburg, Germany
Maritime transportation dominates global trade, with oceangoing ships, including container vessels, bulk carriers, and tankers, handling most of the freight. However, these large, human-made vessels require substantial energy, primarily generated by diesel engines. This reliance on diesel engines has contributed significantly to CO2 emissions, prompting the International Maritime Organization (IMO) to mandate emission reductions across the shipping industry. To address this, two primary approaches are being explored: the adoption of alternative fuels, such as ammonia, and hydrodynamic retrofitting of ships. The latter includes innovations like Air Lubrication Systems (ALS) and wind-assisted propulsion technologies.
Hydrodynamic retrofitting solutions have garnered significant interest, driving companies and industries to develop new methods for implementing these technologies on ships. However, engineering the setup for each vessel must be tailored in advance, as each ship exhibits unique hydrodynamic behavior. Therefore, before installing retrofitting technologies, a thorough understanding of the related fluid dynamics is essential. This requires a hydrodynamic study of ships equipped with such systems, which can be performed either via numerical modeling of the air-water (+bubble) flow around the vessel or via physical experiments, such as towing tank tests. Unfortunately, our understanding of the flow dynamics around ships with air-lubrication systems—one of the most promising retrofitting solutions—remains limited, as research in this area has only gained momentum in recent years.
To better understand the problem and move towards numerical modeling, it is essential to first review the foundational literature, beginning with early studies from the 1970s. However, the Air Lubrication System was proposed a century ago, in 1907 Frederick W. Lanchester [1] explored how aerodynamics and fluid mechanics could be applied to watercraft to minimize resistance, laying the groundwork for later research on air lubrication systems. Most of these studies introduced the concept of drag reduction on wet surfaces through bubble generation. Initial experiments were conducted in tunnels or tanks, where symmetric submerged bodies, such as submarines, were tested to observe frictional drag reduction. This early research sparked more practical studies, where scholars tested ships equipped with air-bubble generators on their hulls in towing tank experiments. While experimental research in this field has provided valuable insights, it is limited in scope, and conducting new experiments for each design can be prohibitively expensive. This is why numerical simulations done using Computational Fluid Dynamics (CFD), have become favored for conceptualizing, and engineering such systems in the early stages. Although CFD modeling of fluid flow around ships without air lubrication has been extensively studied over the past decades, research on ships equipped with air lubrication systems (ALS) remains limited. Replicating this problem in a CFD environment is particularly challenging due to the complexity of the system and the various methods needed to solve it. Furthermore, few studies have transparently reported CFD simulations of ALS-equipped ships. To address this gap, this article presents a CFD-based study on ships equipped with ALS, offering new findings that can assist other researchers in modeling this problem.